Exploring the Best Warehouse Automation Systems of 2025: Revolutionizing Logistics with Smart Solutions and Robotics
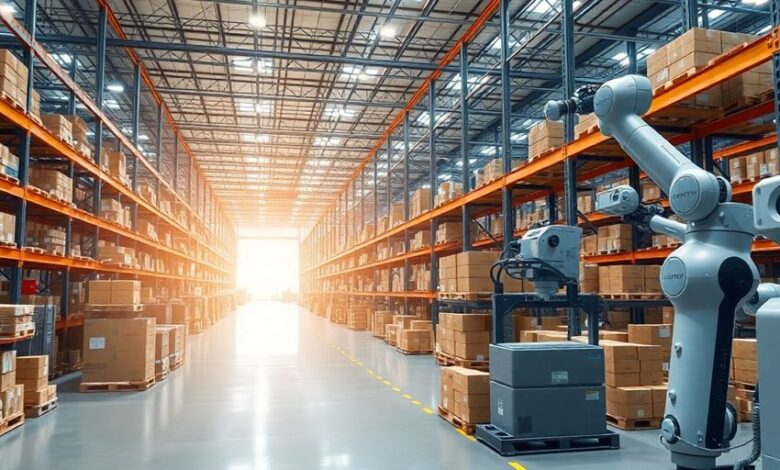
As we step into 2025, warehouse automation systems are changing the game in logistics. With the rise of smart technologies and robotics, warehouses are becoming more efficient and responsive to the demands of e-commerce and global supply chains. This article explores the latest innovations and trends in warehouse automation, shedding light on how businesses can leverage these advancements to stay competitive and meet customer expectations.
Key Takeaways
- Warehouse automation systems in 2025 are heavily reliant on AI and robotics to streamline operations and enhance efficiency.
- Collaborative robots are set to work alongside human workers, improving productivity and safety in warehouse environments.
- Automated storage and retrieval systems are becoming essential for optimizing space and inventory management.
- Sustainability is a growing focus, with eco-friendly technologies being integrated into warehouse operations.
- Warehouse management systems are crucial for coordinating automation technologies and ensuring smooth logistics operations.
Transforming Logistics With Smart Warehouse Solutions
Warehouses are changing fast. It’s not just about storing stuff anymore; it’s about moving things quickly and smartly. The old ways of doing things just can’t keep up with today’s demands. We need to look at how technology can help.
The Role of AI in Warehouse Automation
AI is becoming a big deal in warehouses. It can help with everything from managing inventory to predicting demand. Think about it: AI can analyze tons of data to figure out the best way to store items, plan routes, and even schedule maintenance. This means less wasted time and fewer mistakes. It’s like having a super-smart assistant that never sleeps. For example, AI can help with efficient inventory management by conducting rapid and accurate cycle counts.
Benefits of Robotics in Warehousing
Robots are not just for factories anymore. They’re showing up in warehouses to do all sorts of jobs. They can move heavy boxes, pick items off shelves, and even pack orders. This not only speeds things up but also makes the workplace safer for human workers. Plus, robots can work around the clock without getting tired. It’s a win-win.
- Increased throughput
- Reduced labor costs
- Improved safety
Integrating Smart Technologies for Efficiency
It’s not enough to just have AI or robots. The real magic happens when you put everything together. This means connecting all your systems so they can talk to each other. For example, your warehouse management system (WMS) should be able to communicate with your robots and your AI-powered planning tools. When everything works together, you get a warehouse that’s super efficient and can adapt to changing conditions quickly. This integration transforms how workers perform daily tasks, making it easier to scale labor efficiency and improve accuracy. Consider how SaaS WMS transforms warehouse operations.
Integrating smart technologies is about creating a connected ecosystem. This involves combining AI, robotics, and data analytics to optimize every aspect of warehouse operations. The goal is to achieve a level of efficiency and responsiveness that was previously unattainable, leading to significant cost savings and improved customer satisfaction.
Innovations in Warehouse Robotics for 2025
Warehouse robotics are getting a major upgrade! It’s not just about replacing human workers anymore; it’s about creating systems that work with people and adapt to changing needs. We’re seeing some really cool advancements that are set to change how warehouses operate.
Collaborative Robots and Their Impact
Cobots are becoming increasingly common. These robots are designed to work alongside humans, not replace them. They’re great for tasks that are repetitive or physically demanding, like moving heavy boxes or packing orders. Cobots can adapt to different tasks and environments, making them a flexible solution for warehouses of all sizes. They’re also getting easier to program and use, which is a big plus.
Swarm Robotics for Enhanced Efficiency
Imagine a bunch of robots working together like a team of ants. That’s swarm robotics! These robots can communicate with each other and coordinate their movements to optimize workflows. This is especially useful for large warehouses where goods need to be moved quickly and efficiently. Swarm robotics can reduce congestion, minimize travel time, and improve overall throughput. It’s like having a super-efficient, automated workforce.
AI-Driven Robotics in Fulfillment Centers
AI is making robots smarter and more capable. AI-powered robots can analyze data, learn from their mistakes, and make decisions on their own. This is huge for fulfillment centers, where robots need to be able to handle a wide variety of tasks, from picking and packing to sorting and shipping. AI can also help robots optimize their routes, avoid obstacles, and work more safely. It’s all about making robots more autonomous and efficient.
The integration of AI with robotics is not just about automation; it’s about creating intelligent systems that can adapt to changing conditions and optimize performance in real-time. This will lead to significant improvements in efficiency, accuracy, and safety in warehouse operations.
Here’s a quick look at how AI is improving warehouse operations:
- Improved demand forecasting
- Optimized inventory levels
- Real-time operational adjustments
Automated Storage and Retrieval Systems Revolution
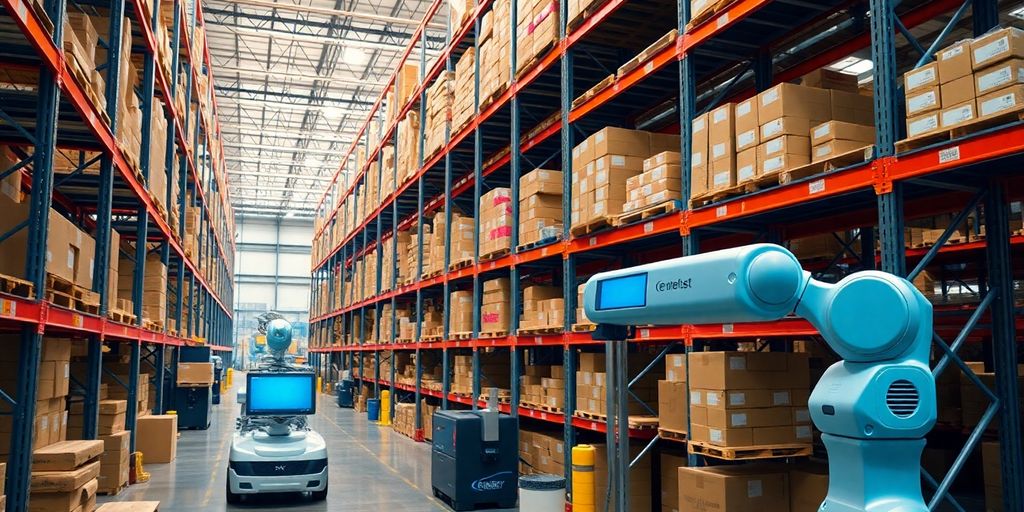
Warehouse operations are undergoing a massive transformation, and at the heart of it all is the revolution in Automated Storage and Retrieval Systems (AS/RS). These systems are no longer a futuristic concept; they’re a present-day reality, reshaping how warehouses manage inventory, space, and order fulfillment. It’s not just about automation; it’s about creating smarter, more responsive, and more efficient logistics ecosystems.
Key Features of Modern ASRS
Modern ASRS are characterized by their ability to maximize space utilization, increase throughput, and reduce labor costs. They come in various forms, including unit-load AS/RS, mini-load AS/RS, and vertical lift modules (VLMs), each designed to cater to specific warehouse needs. Key features include:
- Real-time inventory tracking: Knowing exactly what you have and where it is, at any given moment.
- Automated material handling: Reducing the need for manual labor and minimizing errors.
- Modular design: Allowing for easy expansion and adaptation to changing business needs.
- Advanced control systems: Optimizing storage and retrieval processes for maximum efficiency.
Benefits of Automated Storage Solutions
Implementing automated storage solutions brings a whole host of benefits. For starters, you can significantly increase storage density, allowing you to store more inventory in the same amount of space. This is especially important as real estate costs continue to rise. Other benefits include:
- Improved order accuracy: Reducing errors in picking and packing.
- Faster order fulfillment: Getting orders out the door quicker.
- Reduced labor costs: Automating tasks that were previously done manually.
- Enhanced safety: Minimizing the risk of accidents and injuries.
Automated storage solutions are also proving to be a game-changer in mitigating supply chain disruptions. By enabling warehouses to hold more inventory on hand, businesses can better weather unexpected events and maintain consistent service levels.
Future Trends in Retrieval Technologies
Looking ahead, retrieval technologies are set to become even more sophisticated. We’re talking about things like:
- AI-powered robots: Using machine learning to optimize retrieval routes and improve efficiency. automated storage and retrieval system (ASRS) are becoming more common.
- Swarm robotics: Deploying fleets of robots that work together to fulfill orders.
- 3D printing: Creating custom packaging and components on demand.
And let’s not forget about the increasing integration of ASRS with other warehouse systems, such as Warehouse Management Systems (WMS) and Transportation Management Systems (TMS). This integration will create a more seamless and connected logistics ecosystem, enabling businesses to respond to changing customer demands with greater agility and speed. Pallet shuttles are also becoming more advanced.
Sustainability in Warehouse Automation
It’s not just about speed and efficiency anymore; warehouses are also under pressure to be green. Let’s look at how automation is helping to make warehouses more sustainable.
Eco-Friendly Technologies in Warehousing
Warehouses are starting to use all sorts of eco-friendly tech. Think energy-efficient robots, solar panels, and even green building designs. The goal is to cut down on the environmental impact of running a warehouse. For example, some warehouses are using automated systems that optimize packaging, so they don’t waste materials. Others are using AI and machine learning to predict how much energy they’ll need, so they’re not using more than necessary.
Energy Management Systems for Efficiency
These systems are all about using less power. They use AI to adjust things like lighting, heating, and how machines operate based on what’s actually needed in real-time. It’s like having a smart thermostat for the whole warehouse. This not only saves energy but also reduces costs. Plus, better inventory forecasting means less waste and fewer excess items sitting around.
Circular Supply Chain Practices
This is where things get really interesting. It’s about rethinking the whole supply chain to reduce waste and reuse materials.
Here are some key aspects:
- Using sustainable packaging materials.
- Implementing return programs for products and packaging.
- Optimizing shipping routes to reduce fuel consumption.
By embracing circular supply chain practices, warehouses can minimize their environmental footprint and contribute to a more sustainable future. It’s about closing the loop and making sure resources are used responsibly.
Ultimately, sustainability in warehouse automation isn’t just a trend; it’s a necessity. It’s about finding ways to be efficient, cost-effective, and environmentally responsible all at the same time.
Warehouse Management Systems: The Backbone of Automation
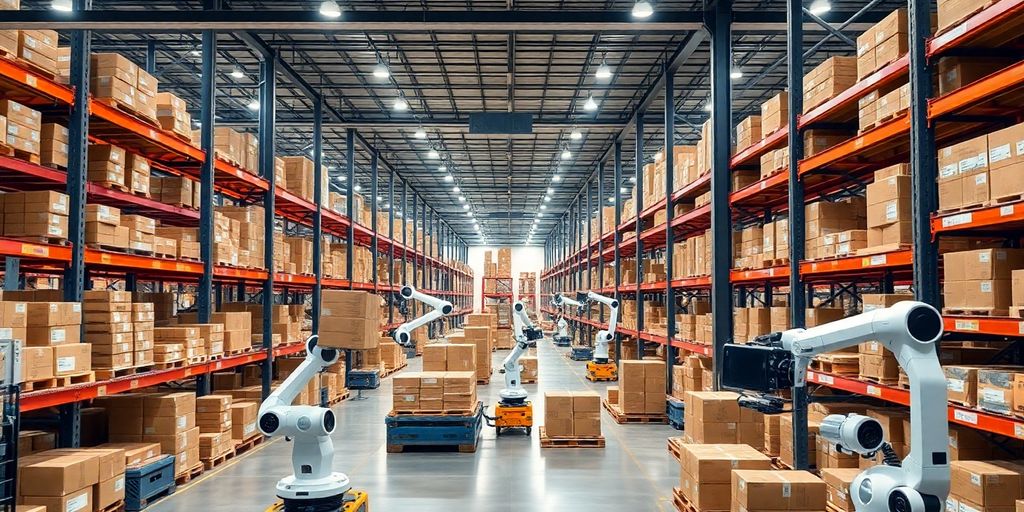
Warehouse Management Systems (WMS) are really important for running modern warehouses. They’re like the brain that controls everything, making sure all the different parts work together smoothly. Without a good WMS, even the fanciest robots and automated systems won’t be as effective. These systems handle everything from tracking inventory to optimizing workflows, and they’re constantly evolving to meet the changing needs of the logistics industry. It’s not just about knowing what you have; it’s about knowing where it is, how quickly you can get to it, and how to use your resources in the best way possible. The right WMS can make or break a warehouse’s efficiency.
Choosing the Right WMS for Your Needs
Picking the right WMS is a big deal. There are tons of options out there, and what works for one warehouse might be a disaster for another. You need to think about the size of your operation, the types of products you handle, and your specific goals. A small warehouse might be fine with a basic, cloud-based system, while a huge distribution center will need something much more robust and customizable. Consider things like scalability, integration capabilities, and the vendor’s reputation. Don’t just go for the cheapest option; think about the long-term value and how well the system will grow with your business. It’s also a good idea to get input from your team – they’re the ones who will be using the system every day. Think about the warehouse automation trends that are coming up.
Integrating WMS with Robotics
Getting your WMS to play nice with your robots is key to unlocking the full potential of automation. It’s not enough to just have robots running around; they need to be coordinated and directed by the WMS. This means making sure the two systems can communicate seamlessly, sharing data in real-time. For example, the WMS needs to be able to tell the robots where to pick items, where to store them, and how to optimize their routes. Integration can be tricky, but it’s worth the effort. When it’s done right, you’ll see big improvements in efficiency, accuracy, and throughput.
Future Developments in Warehouse Management
The future of WMS is all about AI, machine learning, and even more integration. We’re talking about systems that can predict demand, optimize workflows on the fly, and even learn from their mistakes. Imagine a WMS that can automatically adjust its strategies based on real-time data, anticipating bottlenecks and preventing problems before they even happen. This level of intelligence will be a game-changer for the logistics industry, allowing warehouses to operate with unprecedented efficiency and agility. We’ll also see more emphasis on cloud-based solutions, mobile access, and user-friendly interfaces. The goal is to make WMS more accessible and easier to use, so that everyone in the warehouse can benefit from its capabilities.
WMS is becoming more than just a software system; it’s evolving into a strategic asset that can give businesses a competitive edge. By embracing the latest technologies and focusing on integration, warehouses can unlock new levels of efficiency, accuracy, and responsiveness.
Here’s a quick look at how WMS is evolving:
- AI-powered optimization
- Real-time data analytics
- Cloud-based accessibility
Challenges in Implementing Warehouse Automation
Overcoming Technological Integration Issues
Getting all the new automation systems to play nice with what’s already there can be a real headache. A lot of warehouses are still running on older software, and trying to make that talk to the shiny new robots? It’s not always easy. You need a solid plan and maybe even some custom coding to make sure your WMS integrates with robotics without causing a complete meltdown. It’s like trying to fit a square peg in a round hole, but with more expensive consequences if you mess it up.
Training Workforce for Automation
Automation changes the game for your employees, and not everyone is going to be thrilled about it. You can’t just drop a bunch of robots on the floor and expect everyone to know what to do. Proper training is key. You’ll need to teach people how to work with the new systems, how to maintain them, and how to troubleshoot when things go wrong. It’s a big investment in time and resources, but it’s essential for a smooth transition. Plus, addressing employee concerns about job security is crucial to avoid resistance and maintain morale.
Managing Change in Warehouse Operations
Implementing automation isn’t just about installing new tech; it’s about completely rethinking how your warehouse works. That means changing processes, workflows, and even the physical layout of your facility. It can be disruptive, and it requires careful planning and communication to avoid chaos. You’ll need to:
- Develop a clear roadmap for the transition.
- Communicate the benefits of automation to your team.
- Be prepared to adapt and adjust your plans as you go.
Change management is often the most overlooked aspect of warehouse automation, but it’s arguably the most important. If you don’t get your team on board, your fancy new robots aren’t going to do you much good.
The Future of Logistics Automation
The logistics world is changing fast. It’s not just about moving boxes anymore; it’s about using smart tech to make everything work better, faster, and cheaper. We’re talking about a future where warehouses are run by robots and AI, and where getting your package is smoother than ever before. It’s a big shift, and companies that get on board early will be the ones that succeed.
Emerging Trends in AI and Robotics
AI and robotics are no longer just buzzwords; they’re the foundation of the next generation of logistics. We’re seeing AI handle tasks like route optimization and predictive maintenance, while robots are taking over warehouse operations. This means fewer errors, faster delivery times, and lower costs. It’s a win-win for businesses and consumers alike. Companies are starting to use custom-built AI solutions to stay ahead.
Impact of 5G on Warehouse Operations
5G is set to revolutionize how warehouses operate. With its high speed and low latency, 5G enables real-time communication between devices, which is crucial for coordinating robots, sensors, and other automated systems. This means warehouses can become more responsive and efficient, adapting to changing demands on the fly. Think of it as the nervous system of the smart warehouse, connecting everything and enabling seamless operation.
Preparing for the Next Generation of Automation
Getting ready for the future of logistics automation isn’t just about buying new tech; it’s about changing how we think about work. It means training employees to work alongside robots, embracing data-driven decision-making, and being open to new ways of doing things. Companies that invest in their people and processes will be the ones that truly embrace these innovations.
The future of logistics is about more than just technology. It’s about creating a more sustainable, resilient, and customer-centric supply chain. By embracing automation and innovation, we can build a logistics system that meets the needs of tomorrow.
Here’s a quick look at how things are changing:
- More robots in warehouses
- AI making smarter decisions
- Faster communication with 5G
Wrapping Up: The Future of Warehouse Automation
As we wrap up our look at warehouse automation in 2025, it’s clear that these smart systems and robots are changing the game. They’re not just fancy gadgets; they’re essential tools for keeping up with the fast-paced world of logistics. With AI and robotics working together, warehouses are becoming more efficient and safer. Companies that jump on this trend will likely see big benefits, like lower costs and happier customers. So, if you haven’t started thinking about automation yet, now’s the time to get on board. The future is here, and it’s automated.
Frequently Asked Questions
What is warehouse automation and why does it matter?
Warehouse automation uses technology like robots and AI to make warehouse work faster and more accurate. It’s important because it helps businesses keep up with customer demands and reduces mistakes.
How do robots improve warehouse operations?
Robots can do many tasks like picking and packing items quickly and safely. They help workers by taking on hard jobs, making the whole operation smoother.
What are the benefits of using AI in warehouses?
AI helps warehouses make better decisions by predicting what items will be needed and managing stock levels. This means less waste and more efficient use of resources.
What should I look for in a Warehouse Management System (WMS)?
When choosing a WMS, consider how easy it is to use, how well it connects with other systems, and whether it can grow with your business needs.
What challenges do warehouses face when automating?
Common challenges include integrating new technology with old systems, training workers to use new tools, and managing changes in how the warehouse operates.
What is the future of warehouse automation?
The future of warehouse automation includes smarter robots, better AI, and faster communication technologies like 5G, which will make operations even more efficient.